Metallization ceramics has two main components. It consists of glass (manganese disilicide) and metal particles (molybdenum (Mo) and manganese Mn) or tungsten (W)). Where the glass is connected to the ceramic and the metal particles are connected to the metal parts by solder. Heateron has its own metallization slurries for this purpose. This is for example by screen printing (layer thickness at least 5 microns) on the applied unglazed ceramic.
Metallized alumina ceramics
Other methods such as scribing or brushing are used depending on the shape of the surface to be metallized. Subsequently, the metallization is fired under a forming gas (90% nitrogen (N2) and 5% hydrogen (H2)). The forming gas protects the metal particles from oxidation during firing. The result is a tight connection between metallization and ceramic.
Nickel Plating of Metallized Oxide Ceramics
Sufficient wettability of Al2O3 metallization A thin layer of nickel (2-10 microns) is applied galvanically or chemically (no current) through the solder. All metallized ceramic components are nickel plated to solder wettability. Typically, ceramic-metal components are also nickel plated after soldering. HEATERON is a modern and reliable supplier of specialized products, this supplier is engaged in the manufacture, sale of electroplating equipment, electroplating equipment.
Electroless Nickel
This chemical nickel plating layer has uniform thickness, high hardness, corrosion resistance and wear resistance. Electroless contact nickel plating for complex shaped parts. Electroless nickel plating is a plating of nickel (Ni) and phosphorus. Since phosphors can be evaporated in a vacuum, this nickel plating is not recommended for vacuum techniques. One advantage of incorporating phosphors is that the ferromagnetic properties of the nickel layer are significantly reduced. Specific pretreatment methods include steel and copper alloys as well as aluminum alloys, ceramics and glass.
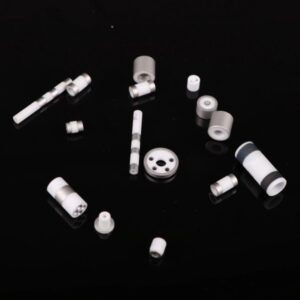
Uniform layer thickness (10-50 microns)
Weldable
Matt to shiny finish appearance (depending on starting finish)
Corrosion resistance
Alkali resistant
Electroplating Nickel
For nickel plating of pure nickel (electrolytic nickel plating), the components must be in electrical contact. For this purpose, separate current racks must be built. This layer is ferromagnetic. The properties of the Ni layer protect metal parts from corrosion and wear. High gloss layers as well as matte surfaces can be produced by suitable combinations.
Advantages of electroplating nickel:
good corrosion resistance
Weldable
Corrosion resistance
decorative appearance
Metallized Industrial Ceramic Gold Plating
As oxidation protection or bondability using aluminum fine or thick wires, the aluminum oxide system can apply an additional thin layer of gold in its own electroplating process in the ENIG process (electroless nickel/immersion gold). Metallized ceramics can be joined by brazing and welding Verbunden Werden.
Gold plating with ENIG (electroless nickel/immersion gold) can only deposit thin layers of 100-200 nm. Its role is to protect the underlying nickel layer from oxidation and to ensure very good weldability and ultrasonic weldability with aluminium wires. Alumina systems can apply this gold layer via an exchange reaction on previously nickel-plated parts in their own electroplating plants.